
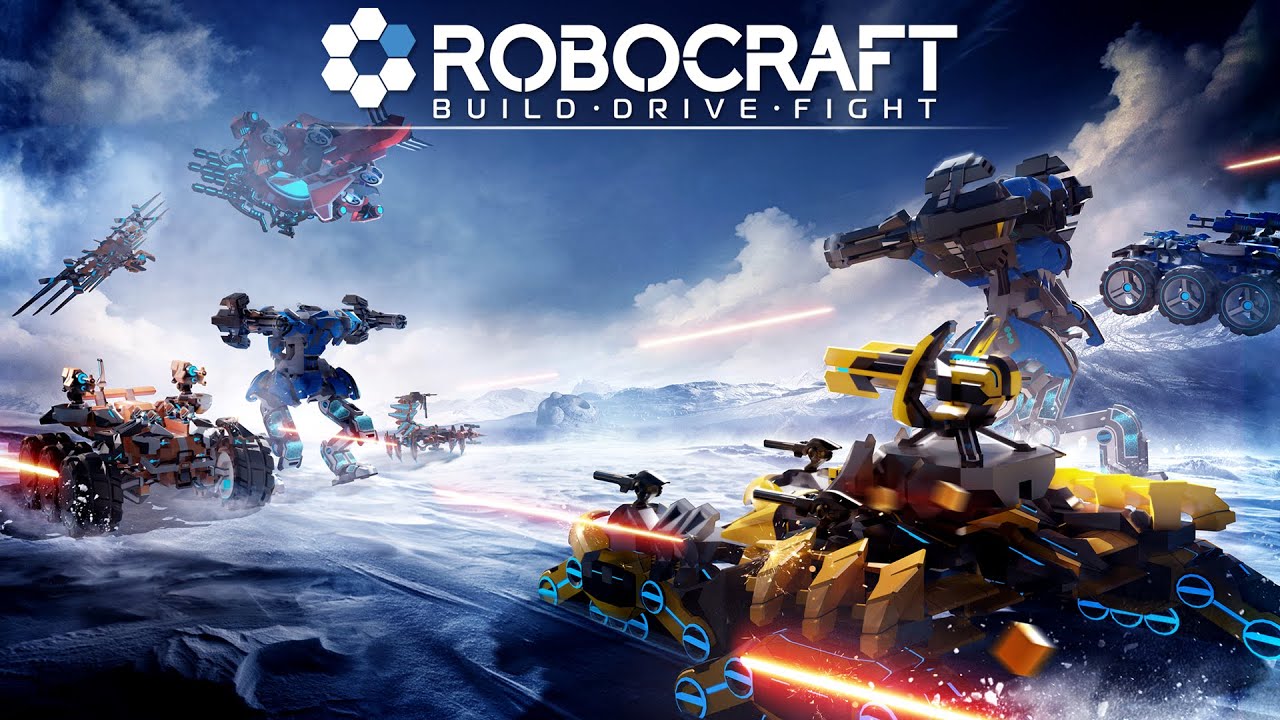
The other 3D printed robot at the competition used acetone to melt the surface in an attempt to increase the strength, but his parts ended up fracturing too. “My parts shattered in situations where many metals would have bent. “The competition proved that a 3D printed weapon and weapon mounts aren’t great,” Hurd tells us. Hurd wanted to test how a Battlebot built from a standard ABS plastice and 3D printed would fare against machines which featured other construction methods and materials, and you can see the results in the video below. Robot fighting can be a violent pastime, and fights are held within an arena constructed of steel, wood, and bulletproof, clear Lexan plastic. The Battlebots can weigh as little as the 75 gram ‘Fleaweight’ class models, but Hurd decided his 3D printed entry would be in the 1 pound – or 454 gram – ‘Antweight’ class. The robots themselves can weigh in at up to 300+ pounds and feature exotic materials and sophisticated electronic designs. Most of the machines are remote-controlled and robot combat has a dedicated following. Robot combat is a hobby in which two or more custom-built machines are designed and built to destroy or disable their opponent. So with that experience behind him, Hurd decided to take on a three-week long challenge to build a Battlebot for competition. “Before, I had never seen a 3D printer, but at college basically every lab has their own MakerBot. “When I came to college, the first thing I tried to do was find a lab that I could work in,” Hurd told. Hurd has won multiple awards, serves as a mentor for FIRST Robotics team 4611, and invented a robot accessory wheel that helps robots navigate varying terrains, and it was his first 3D printed project.
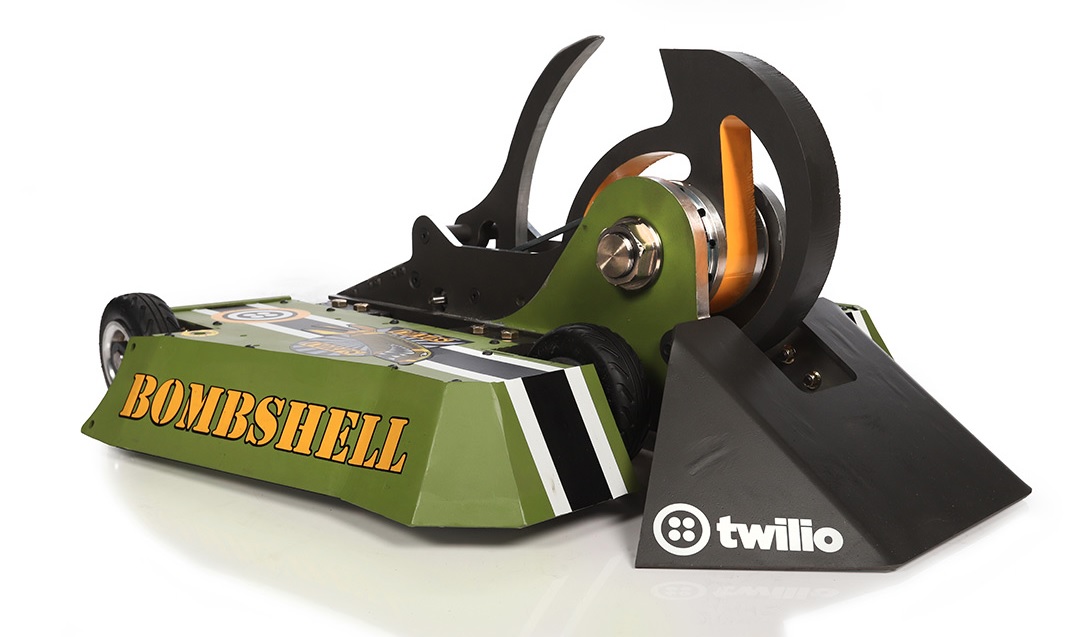

Most of the time the only way to succeed with a smaller budget and limited tools was to have the most clever design. “The National Robotic Challenge became my outlet, and I worked for hours hand shaping and testing different components. “Throughout middle school I continued tinkering and got into art, but when high school rolled around I had a new motivator: winning,” Hurd says. He works with robots in the Design Innovation and Simulation Lab, and he’s also working for Eaton designing and testing mechanisms for electrical-sector products.īut it’s his experience with the various methods of additive manufacturing that led him to build a Battlebot with 3D printing. Carter Hurd is on the way to earning a degree in mechanical engineering at Ohio State University, where he’s a teaching assistant for the Fundamentals of Engineering Honors program.
